Since the beginning of Janler in 1952, designing and building custom plastic injection molds has been the mainstay of our business.
Working with our customer in the early development stages of the design to ensure a seamless transition to final production.
Mold Making
With innovations such as the world’s first unscrewing stack mold, Janler continues a long tradition of supplying cutting-edge solutions to the plastics industries. We specialize in tight tolerance, multi-action mold design and development, and offer a wide range of plastic mold solutions for just about any project no matter the size or complexity.
Capabilities:
Mold Building Plant
Our tool shop includes multiple machining centers and a full-service EDM department. We invest in the latest CNC and EDM technologies to stay at the forefront of plastic injection mold manufacturing. Before shipment we test, sample and qualify each mold against customer requirements to ensure that all aspects of design, documentation and processing have been met satisfactorily.
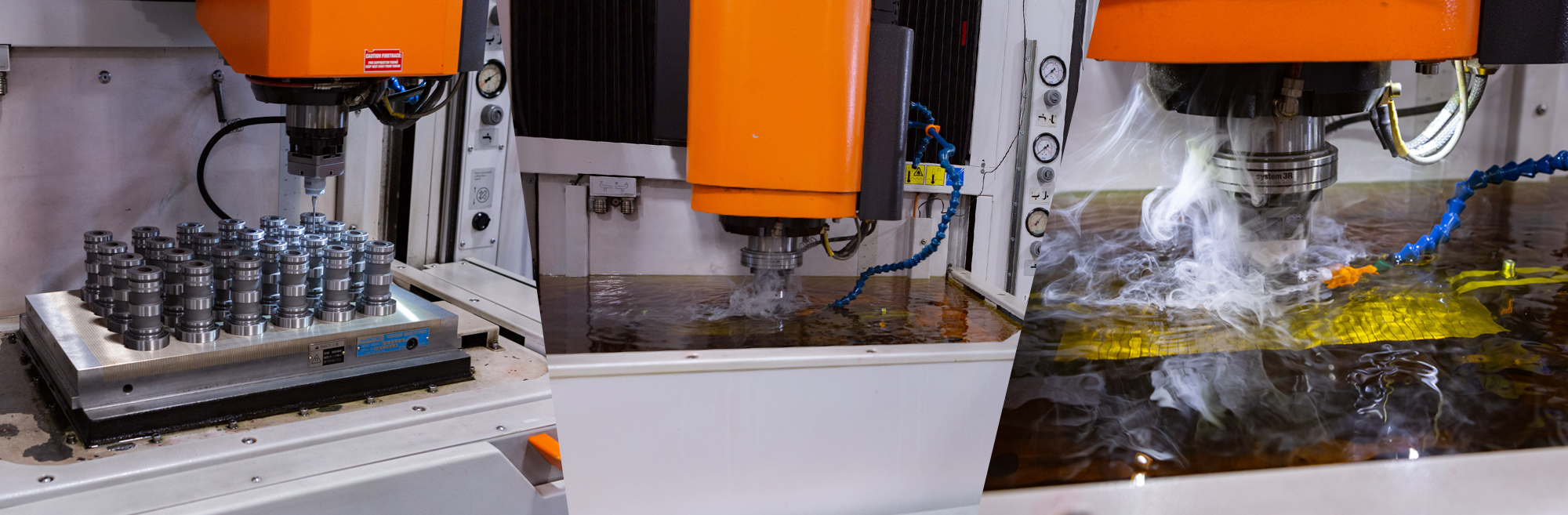
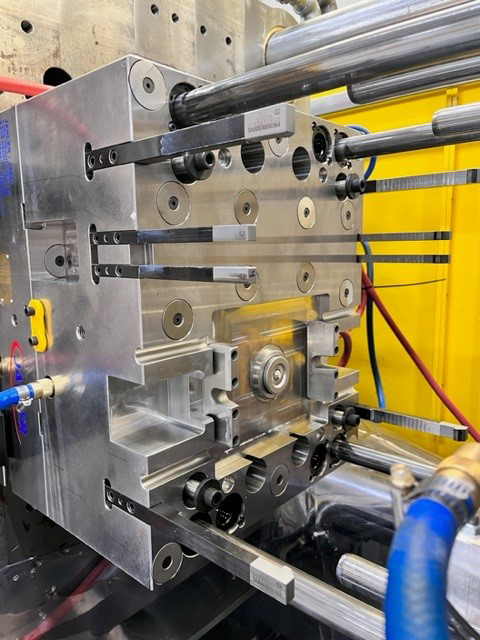
Pre-production/Production Molds
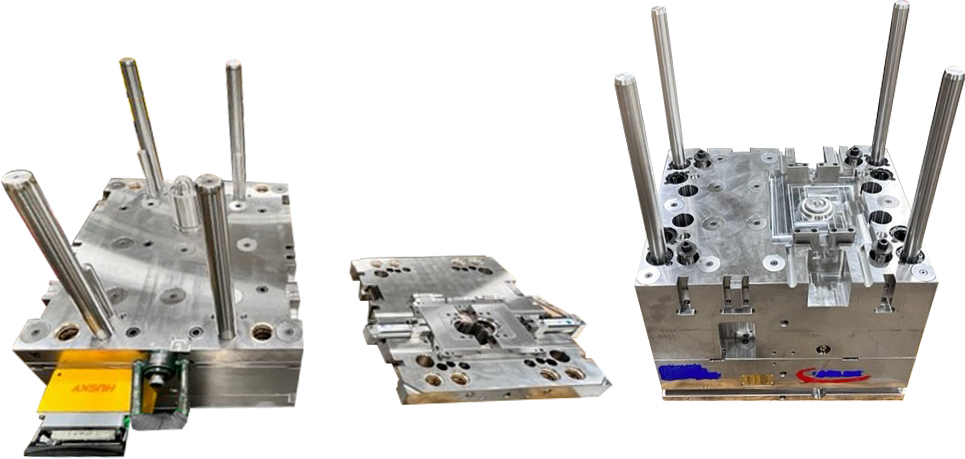
Whether it’s manufacturing a pre-production mold or a full production mold, Janler has the experience and expertise necessary to build the most appropriate molds to accomplish customer goals.
We consider prototyping to be a valuable step in the mold manufacturing process, and it is usually one that should not be skipped. Before making the considerable investment in a high cavitation production mold, valuable lessons can be learned by molding samples on a prototype mold that replicates the exact conditions of the production mold. A prototype mold can also bridge the requirement for production while the production mold is being manufactured.
When the time comes for a production mold Janler taps into the knowledge gained from over 70 years of mold manufacturing and utilizes the latest technologies to deliver the highest quality molds on time and within budget.
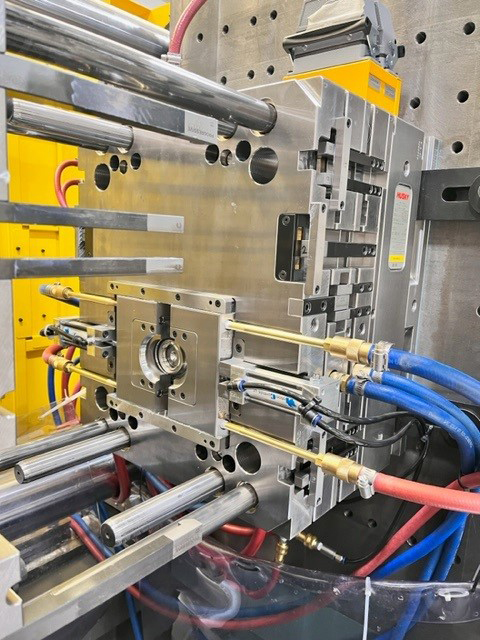
Low to High Cavitation Molds
The process of determining how many cavities per mold will optimize your productivity can be daunting. Whether to go with a low cavity mold or a high cavitation mold depends on your specific application.
A low cavity mold will have a shorter lead time and they are comparatively inexpensive, but in the end there will be a higher price per piece. This is generally most appropriate when the production quantities are low or for prototype molds.
Going with a high cavitation mold will be more expensive at the onset, but the resulting price per piece will be lower due to economies of scale. This becomes more and more appropriate with higher production quantities.
Janler works closely with customers to find the right balance and determine the optimum cavities per mold based upon the specific needs of each customer and their application. Experienced and adept at low cavity to high cavity molds, Janler maintains the highest precision, repeatability and cost-effectiveness no matter how many cavities are involved.
Multi-Action Molds
Certain mold features, like undercuts and holes, may require the use of actuated mechanisms. Janler has vast experience incorporating one or more actions and effectively adjusting mold construction to best accommodate the required actions. Multiple side action features are commonplace on Janler molds.
Insert Molds
Injection molding around an insert (usually metal) is a common process, but requires experience to perform effectively. Janler is very accustomed to insert molding and to manufacturing molds for insert molding. Taking the knowledge gained from contract insert molding and translating it into an effective and efficient insert mold design, Janler develops the most appropriate molds for any given application.
In-Mold Closing
Designing systems that can automatically assemble molded parts before ejection, Janler assists customers reduce costs through the reduction of post molding assembly. Fast cycle times can be maintained since the actuation occurs during mold opening and ejection.
Combination/Family Molds
Combining non-identical parts in multiple cavities within a single mold can save time and reduce costs. However, it must be done right and take into account a variety of different factors in order to be effective. Janler has a long history of manufacturing combination/family molds and has the necessary expertise to design it correctly and maximize efficiencies.